Rotational Molding
Production rotomolding involves the transformation of plastics using temperature and rotation. The hollow, plastic parts are formed by the addition of resin into an open mold. Secondly, the mold is then closed, heated, and cooled while continuously and slowly rotating on one or more axis. Fibeco specializes in custom rotational molding, which allows us to produce a wide range of parts, specifically low volume and complex parts. In addition, Fibeco can help you with custom rotomolding solutions from product design to secondary finishing.
Prototype Rotational Molding
Fibeco has developed its own rotational molding process for prototypes. This process has been completed by creating set-ups in house to produce production-quality hollow, plastic rotationally molded prototype parts for customers to test form, fit, and function before investing in production.
Commonly Used Materials
Resin
Resins differ depending on part requirements, such as strength and flexibility. Fibeco has experience usingresins including but not limited to: LLDPE, Repro, MDPE, HDPE, XLPE, PVC, PP, Acetal, Hytrel, Soft Touch, Nylon resins, and Nylene 494.
Polyurethane Foam Filling
Depending on the industry and requirements of a product, polyurethane foam filling has been used for insulation, cushioning, structure, and/or part rigidity.
Inserts, Rivets, & Rivnuts
If required, inserts, rivets, and rivnuts in a variety of shapes and sizes will be be molded-in (encapsulated), or installed post molding.
Mold-In & Mold-On Graphics
Mold-in graphics are molded onto a part during the molding process, and mold-on graphics are molded onto a part after the demolding process. Both mold-in and mold-on graphics are a great alternative for rotomolding rather than stickers or decals due to a more permanent bond to the part.
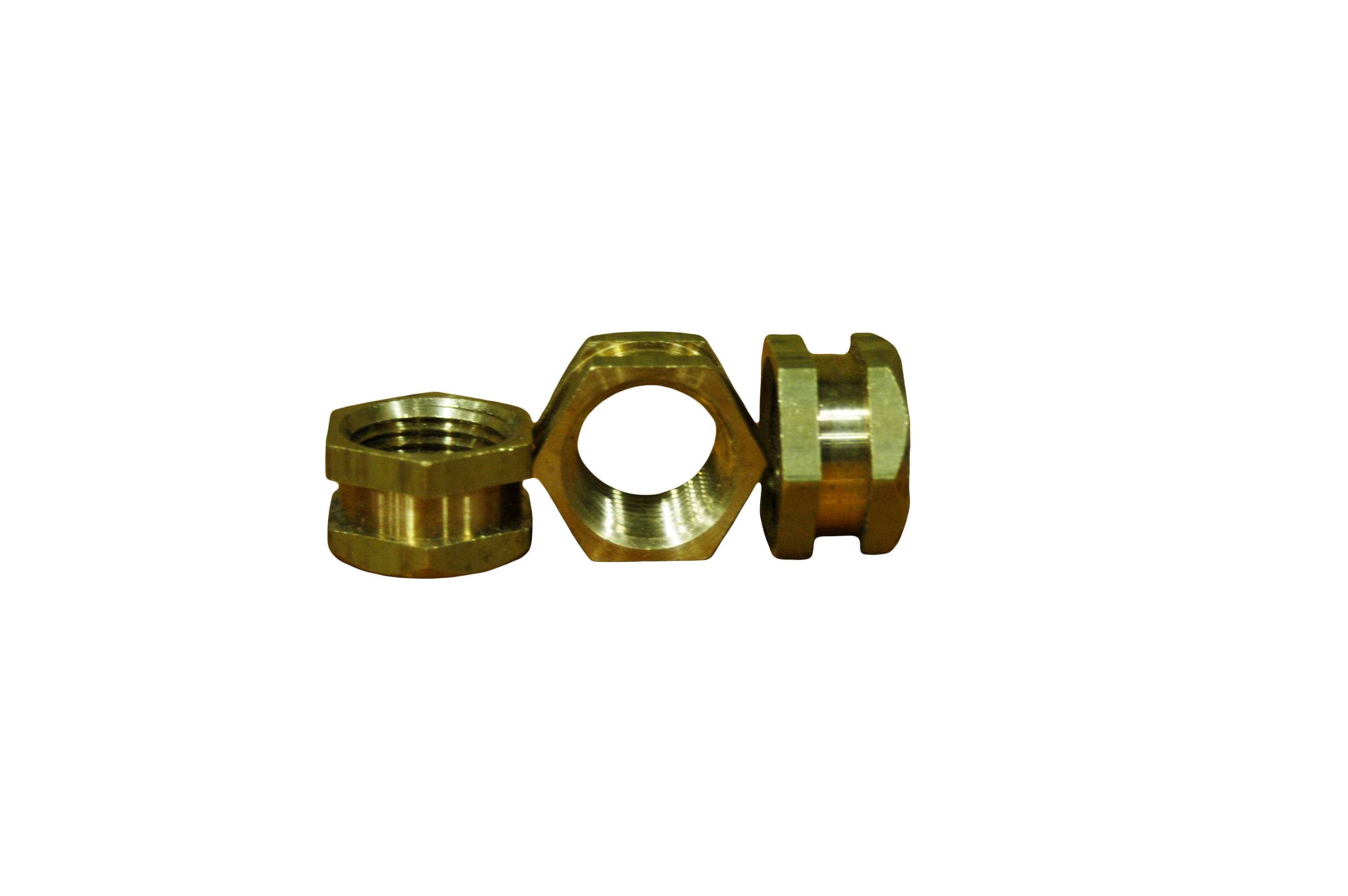
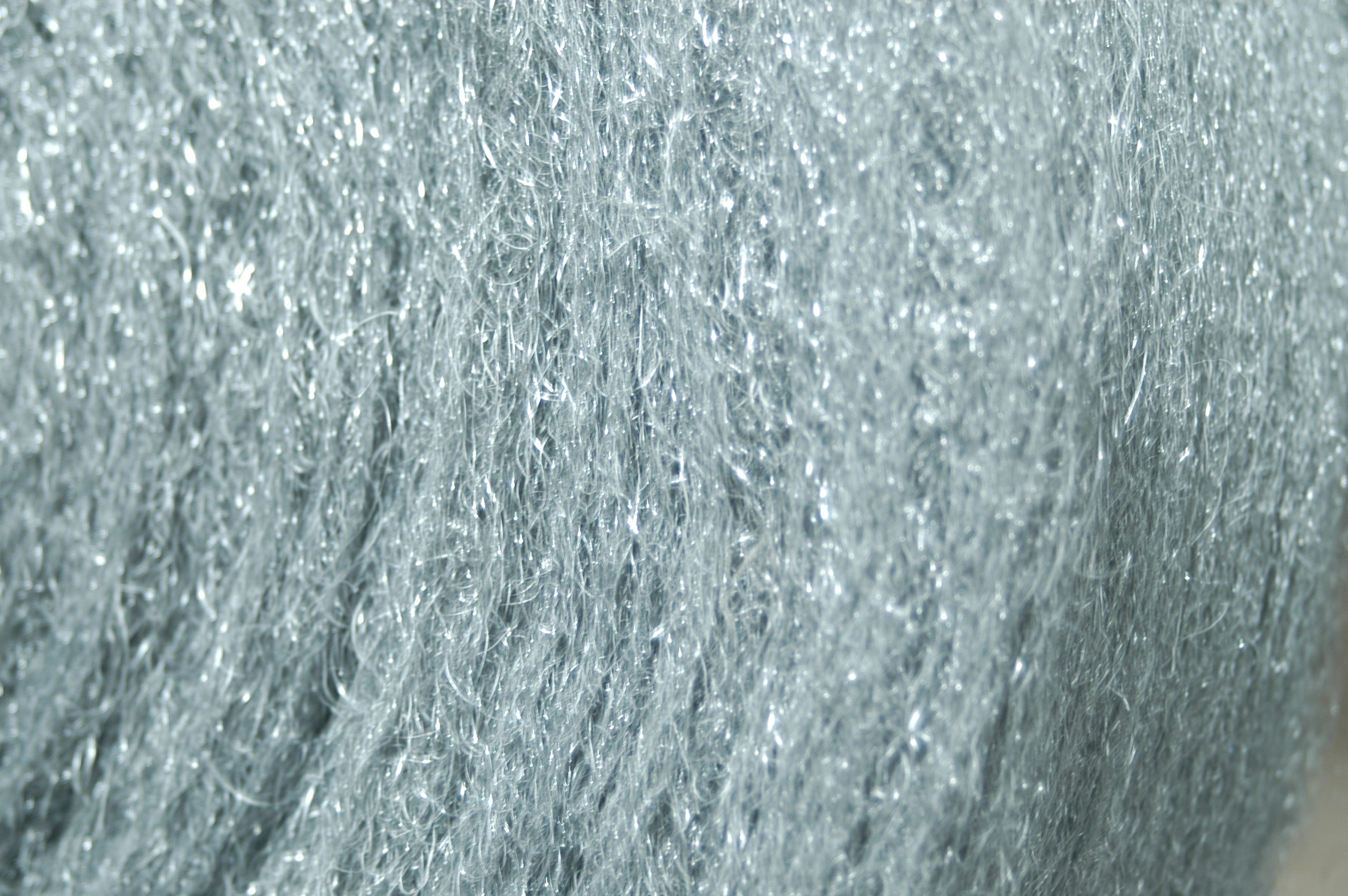
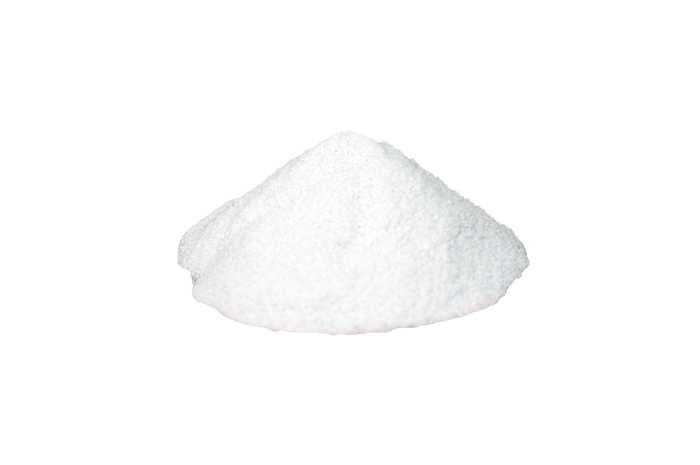
Quality Checks
Leak/Pressure Testing
Air will be blown into parts to a certain PSI, the part is then submerged in water and inspected for air bubbles to maintain leak-proof parts.
Part Measurements
Production parts as well as part fittings and sub-assemblies will be constantly measured to guarantee uniformity among all alike parts.
Part Internal Air Temperature
An internal temperature logger will be used to trace PIAT throughout the rotational molding process ensuring curation.
Wall Mapping
The nominal wall thickness of part surfaces will be mapped and documented to ensure consistency, eliminating potential weak spots.
Rotational Molding Pros
Design Flexibility
Rotational molding has the ability to produce complex designs that may otherwise be difficult to replicate using other production processes, as well as the ability to mold simple designs.
Size Variety
Rotational molding allows a large variety in part sizes, with the ability to mold parts the size of a tennis ball to 1,000 gallon solution tanks.
Materials
Plastic products can provide better properties than competing materials such as metals. When converting metals to plastics, plastics allow higher impact strength, weather resistance, and efficiency in weight reduction and cost savings.
100″
machine molds up to a 100″ diameter
40+
years of combined experience
5
axis CNC center for trimming parts
2
in house rotomolding machines